Cylinder Washing and Drying Unit
The Cylinder Washing and Drying Unit is essential for ensuring the cleanliness and safety of cylinders before they are filled with gas. This unit typically operates inline with the conveyor system, facilitating a seamless and efficient process.
Key Features
- Washing Mechanism: Utilizes multiple high-pressure water jets or to remove contaminants such as dirt, oil, and residues from the exterior of the cylinders
- Drying Process: forced air systems to dry the cylinders post-washing, preventing any residual moisture that could affect the filling process.
- Automation: Designed for unmanned, continuous operation, these systems are integrated with the plant's chain conveyor, allowing cylinders to move seamlessly from washing to drying stages.
LPG Cylinder Purging Units
We supply high-quality LPG Cylinder Purging Units designed to safely replace atmospheric air with LPG vapour in cylinders before filling. This process eliminates the risk of explosive mixtures and ensures compliance with safety standards.
Key Features
- PLC-Controlled Automation: Our purging units are equipped with Programmable Logic Controllers for precise and efficient operation.
- High Capacity: Designed to handle up to 1,200 cylinders per hour, suitable for both small and large-scale bottling operations.
- Explosion-Proof Design: Constructed with flameproof enclosures to meet safety standards in hazardous environments.
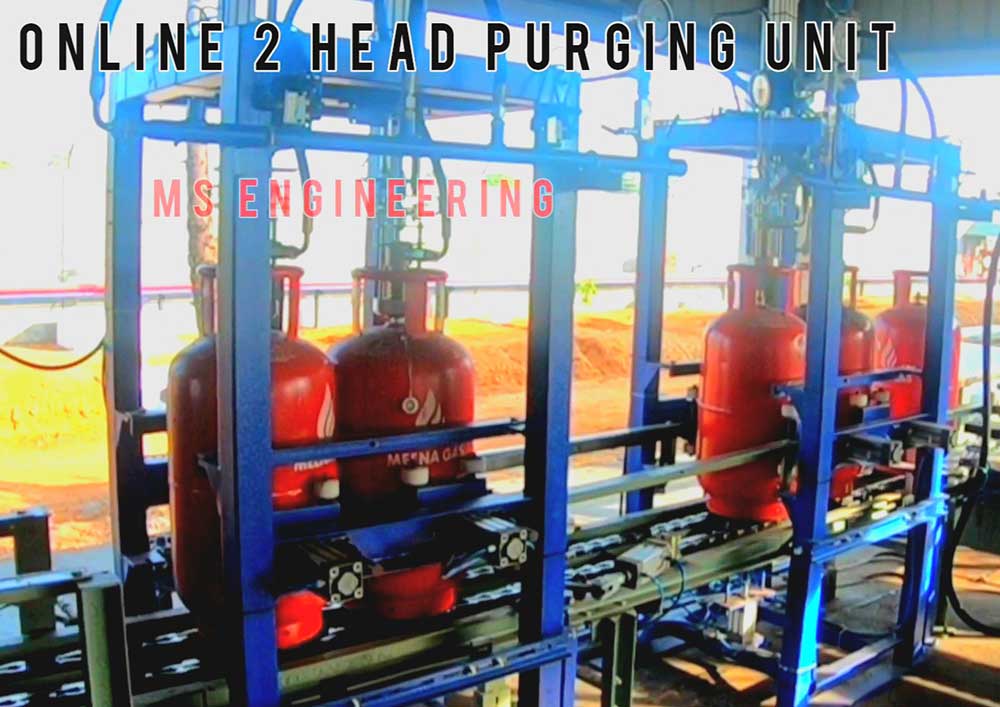
Inline LPG cylinder filling units
We supply LPG cylinder filling units designed for efficient and safe filling operations in bottling plants. Our systems are engineered to handle cylinders ranging from 4 kg to 50 kg, and also 425kg catering to various industrial and commercial needs. We have the centralized tare weight system with multiple conveyor line. Available in manual, semi-automatic, and automatic configurations.
Key Features
- Electronic Load Cell-Based Filling: Ensures precise filling by weight, with tare weight entry via a user-friendly keypad.
- Automation: Features automatic engagement and disconnection of filling heads, minimizing manual intervention.
- Explosion-Proof Design: Constructed with flameproof components suitable for hazardous environments.
- Compliance: Meets international safety standards, including ATEX and PESO approvals
- Filling Accuracy; 99% (± 50 gms.)
- Dual Flow Cut off for Coarse and Fine filling.
- Air Pressure 5 bar.
- LPG Pressure 13-15 bar.
- Safety Interlocks.
- Coloured HMI Display for Net, Tare, Gross Weights, Status and Error Display.
- Suitable for 25mm/22mm SC Valve.
- Centralized tare weight system for multiple lines.
Filling Capacity for 14.2 Kg Cylinder | |
---|---|
6 Point | 450 cylinders per hour. |
10 Point | 650 cylinders per hour. |
12 Point | 800 cylinders per hour. |
Check Scale
Ensure every LPG cylinder is filled with pinpoint accuracy using our industrial-grade check scales. Designed for speed and reliability, they seamlessly integrate into high-volume bottling lines. Built tough for long-term use, they help maintain safety and compliance effortlessly.
Key Features
- High-Precision Weighing for consistent fill levels
- Rugged & Fast Operation ideal for demanding plant environments
Automatic Weight Correction
We offer advanced Automatic Weight Correction Units designed to ensure precise and compliant LPG cylinder filling in bottling plants. These systems automatically adjust the weight of underfilled or overfilled cylinders, enhancing operational efficiency and safety. Available in manual, semi-automatic, and automatic configurations.
Key Features
- Automatic Weight Adjustment: The system detects cylinders with incorrect weights and automatically adds or removes LPG to achieve the desired weight.
- High Accuracy: Offers weight correction with a resolution of 50 grams, ensuring precise filling.
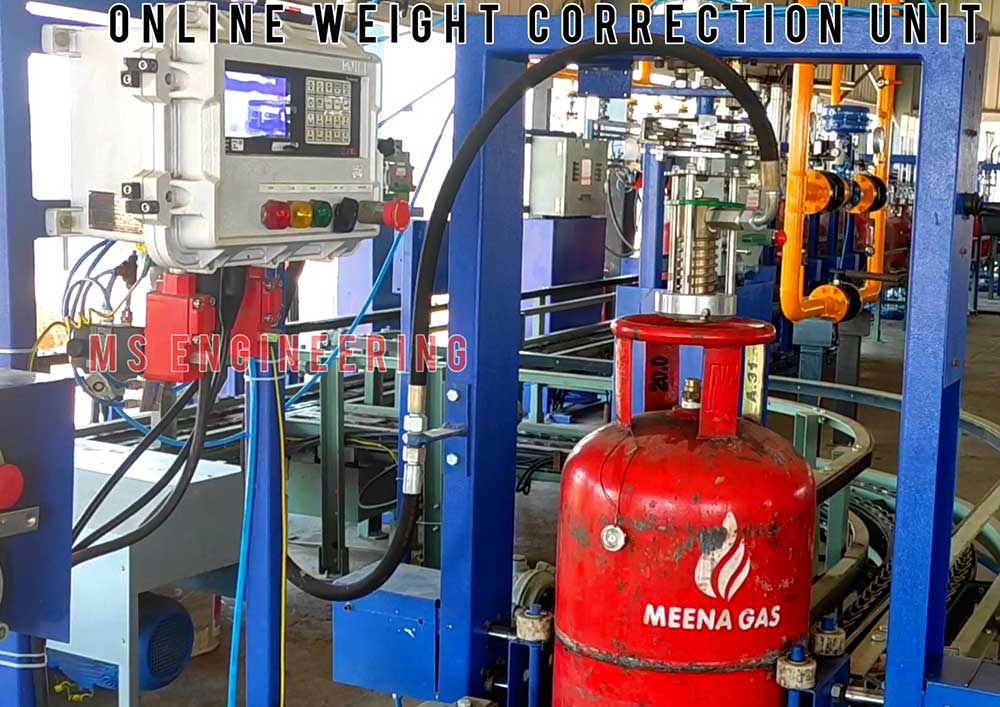
Valve Leak Detection (VLD) & O-Ring Leak Detection (OLD)
Detect Even the Smallest Valve Leaks (0.05 gms/hr) Instantly – Our advanced VLD unit ensures safety and compliance at every stage of LPG bottling, reducing risk and preventing costly gas losses. Available in manual, semi-automatic, and automatic configurations
Precision Detection at the Seal – Our O-ring leak detection system identifies micro-leaks at the cylinder neck seal, enhancing safety and reducing rework in the filling line. Available in manual, semi-automatic, and automatic configurations.
Cylinder Evacuation Unit
An essential component in LPG bottling plants, designed to safely remove LPG from cylinders that are defective, overfilled, or require maintenance. This process prevents the accumulation of hazardous mixtures and ensures compliance with safety standards. Available in manual, semi-automatic, and automatic models.
Key Features
- Safe LPG Removal: Evacuates LPG from cylinders to eliminate the risk of explosive mixtures.
- Automation: Equipped with PLC-controlled systems for precise and efficient operation.
- High Capacity: Designed to handle multiple cylinders simultaneously, enhancing throughput.
Valve Changing Units
- Hydraulic Valve Changing Machine: Employs a hydraulic power pack to provide controlled torque for valve replacement. The machine includes a flameproof motor, manually operated spindle, and pneumatic clamping, ensuring safe and efficient valve changes.
- Inline Valve Screwing Machine: Designed for integration into conveyor lines, this machine offers hydraulic torque control, adjustable height, and a clutch mechanism to fit different cylinder valves. It also includes an external control panel with sensors for ease of operation.
- Available in manual, semi-automatic, and automatic models
Hot Air Sealing Units
We designed for the efficient and safe application of thermoplastic PVC seals around LPG cylinder valves. These units ensure that cylinders are securely sealed, preventing contamination and enhancing safety during storage and transportation
- TWO HEAD - with two gun and seal two cylinders at the time.
- SINGLE HEAD – with single gun and seal one cylinder at the time.
- High Capacity: Designed to handle multiple cylinders simultaneously, enhancing throughput.
Hydro Testing Unit
- Reliable Hydro Test Units for LPG Cylinders – Built for high accuracy, fast throughput, and full compliance with safety standards.
- Test pressure up to 30 kg/cm² or as per requirement
- Available in manual, semi-automatic, and automatic models
- Designed for bulk testing with minimal water consumption
- Integrated with safety interlocks and data recording systems
- Compatible with various LPG cylinder sizes and standards
Pneumatic Testing Unit
- High-Pressure Accuracy, Zero Compromise – Our Pneumatic Testing Unit delivers fast, safe, and reliable leak detection for LPG cylinder.
- Test pressure up to 12.5– kg/cm², adjustable.
- Available in manual, semi-automatic configurations.
LPG Cylinder Dip Bath Unit
An essential component in LPG bottling plants, designed to safely remove LPG from cylinders that are defective, overfilled, or require maintenance. This process prevents the accumulation of hazardous mixtures and ensures compliance with safety standards. Available in manual, semi-automatic, and automatic models.
Key Features
- Safe LPG Removal: Evacuates LPG from cylinders to eliminate the risk of explosive mixtures.
- Automation: Equipped with PLC-controlled systems for precise and efficient operation.
- High Capacity: Designed to handle multiple cylinders simultaneously, enhancing throughput.
Firefighting system
We offer complete fire water fighting systems with automatic sprinklers, integrated with compressor and pipeline solutions for consistent pressure and flow. Our systems are designed to detect and respond instantly to fire, ensuring maximum protection for LPG bottling plants. With seamless pipeline layout and reliable compressor support, you get round-the-clock operational readiness. Ideal for high-risk zones, these systems meet all safety compliance norms.
Key Features
- Automatic Fire Detection & Sprinkler Activation for fast fire suppression
- Integrated Compressor & Pipeline Systems for steady water pressure and reliable coverage
- Designed for Hazardous Environments with durable, industrial-grade components
Gas Monitoring System
Our gas monitoring devices continuously detect LPG leaks in real-time, providing early warnings to prevent accidents. Equipped with high-sensitivity sensors, they immediately trigger alarms when gas concentrations exceed safe levels. These systems also identify and display the exact leakage zone and area on the connected control panel. Ideal for critical points across the plant, they ensure rapid response and enhanced operational safety.
Key Features
- Real-Time LPG Leak Detection with zone-wise identification
- Instant Alarm Activation and display on connected systems
- Seamless Integration with plant control and safety panels
Dp valve
Our fully automatic PLC-based DP valve system is designed to precisely control and maintain the desired pressure during LPG cylinder filling. It ensures smooth operation by automatically adjusting to the set pressure parameters, preventing overpressure or underfilling. The dual-sealing mechanism enhances safety, while real-time monitoring through the PLC system provides instant status and leak alerts. This smart solution reduces manual handling and improves overall plant efficiency.
Key Features
- Automatic Pressure Control to maintain user-set filling pressure
- Dual-Sealing with Leak Detection for maximum safety
- PLC-Based System with real-time monitoring and remote access